Integrated incubators improve your isolated ATMP Cell and Gene production
Integrated incubators are a key part of manufacturing processes for cGMP ATMP Cell and Gene Therapy applications
Most of the Advanced Therapies Medicinal Products (ATMPs) or Cell and Gene Therapy production processes involve cell culture phases under strictly controlled and reproducible conditions.
For this reason, an integrated incubator represents an essential accessory for an isolator designed for cGMP Cell & Gene Therapy applications.
Comecer offers a ATMP - Cell & Gene Therapy incubating system fully integrated with the isolator and believes that this approach is characterized by many advantages for a cGMP production process with respect to stand-alone incubators installed in a classified laboratory.
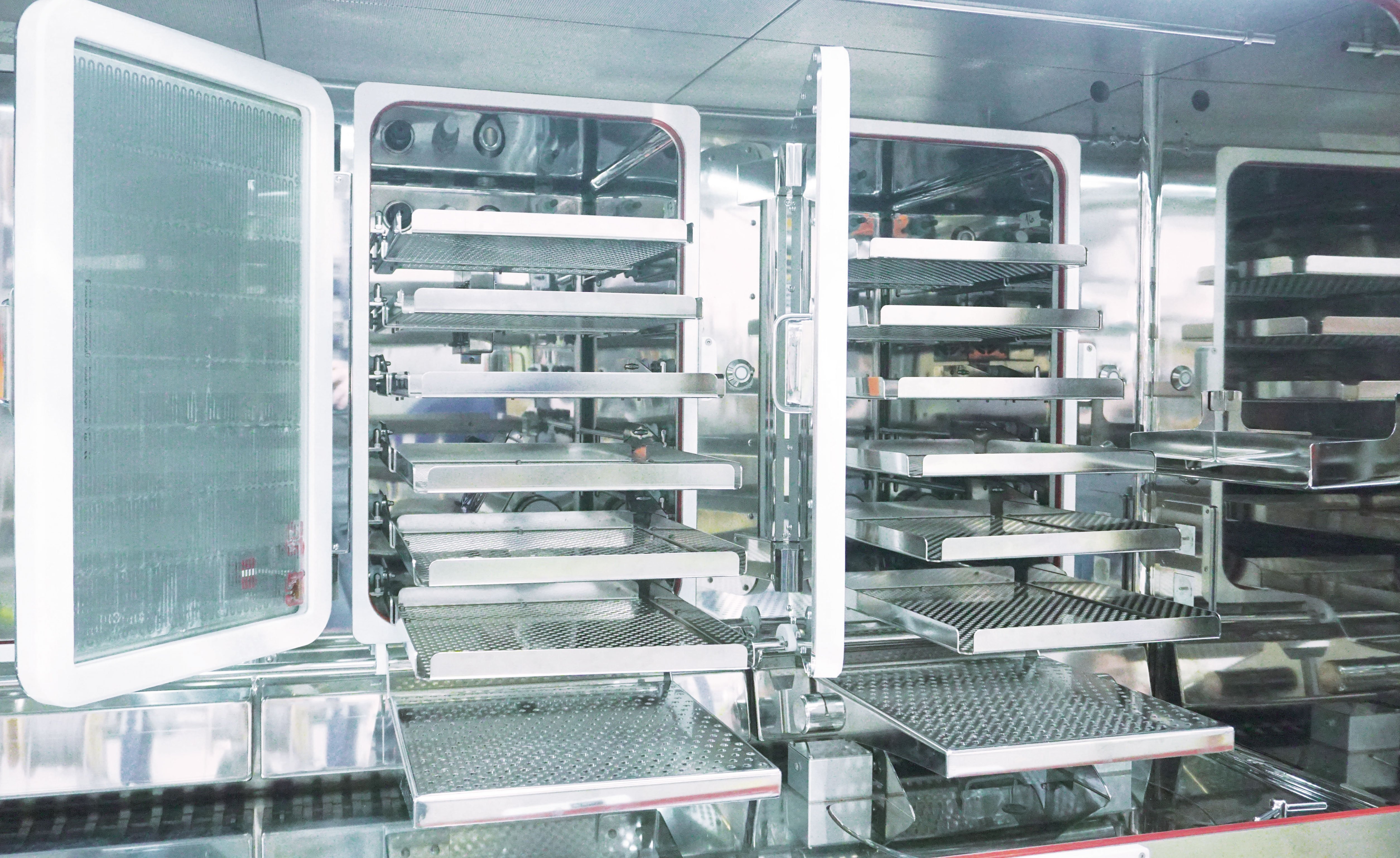
Indeed, it allows the fine control of the main Critical Process Parameters (CPPs):
- Temperature
One of the most important features of an incubator is a precise temperature control. Most cell culture applications require a temperature range between 37°C and 40°C and Comecer incubator can firmly maintain the set temperature target with high accuracy. - Relative humidity
For optimal cell growth, environments require a precise relative humidity management. Through an automatic system, Comecer incubator controls the rH level by directly injecting purified water vapor into the incubator’s volume. Due to the high diversity of cell growing conditions, the operating conditions can achieve values higher than 85% in rH without dew formation on the internal surfaces. - CO2 and O2 concentration control
Cell cultures need a controlled atmosphere in terms of gas concentrations. In most applications, CO2 concentration is typically set at 5% for its buffering effect on the culture medium pH. Regarding O2 concentration, it could range from environmental concentration (21%) to anaerobic conditions based on the culturing conditions.
By means of dedicated injecting systems, Comecer incubator can precisely adjust and maintain the relative gas concentrations to which cell cultures are exposed. - Internal pressure control
A fully integrated system requires a pressure control system between the incubator and the “grade A” working chamber in which the incubator is installed. The differential pressure guarantees a high level of contamination prevention and control. Moreover, the high flexibility of the pressure control system could be exploited for different kinds of applications, whether they were for autologous or allogenic therapies. - Airflow and particulate contamination control
The incubator should have a system that allows proper airflow, which is important for cell growth and preventing condensation. Comecer incubator is characterized by an adjustable air flow rate and a specific ratio of HEPA-filtered air make up.
Moreover, an internal fan is responsible for the maintenance of CPPs homogeneous conditions within the whole incubator volume.
Moreover, the integration with the isolator leads to many functional benefits:
- VPHP decontamination and aseptic condition maintenance
The incubator surfaces are decontaminated by exploiting the same VPHP decontamination cycle of the isolator. The maintenance of the reached aseptic condition is guaranteed by the ventilation system dedicated for the incubator. - Functional and safety integration with the grade A working chamber
Incubator and isolator are also characterized by functional integration; in fact, communication between these two components allows the respect of safety conditions and process quality requirements. - Mechanical integration
The incubator is located on the rear wall of the main chamber; this solution allows to save space in the grade A working chamber, without negatively impacting the operator ergonomic. - Process flexibility
The incubator is typically located on the rear wall of the working chamber but can be integrated on a lateral wall as well, depending on the space available.
Incubator volume could be customized for many different applications, ranging from cell culture to gene editing, from cell reprogramming to differentiation.
These processes require different accessories to be installed inside the incubator volume, such as:- Rocking shaker;
- Orbital shaker;
- Roller bottle.
-
- Bioreactors;
- T-flasks;
- Shake flasks;
- Multilayer systems.
- Less material handling
The integration of the incubator directly in the “grade A” working chamber allows to greatly reduce product and material handling, consequently reducing the risk of contamination or operator mistakes. - Process parameter monitoring system
CPP are continuously monitored by the integrated sensors during the operating phase.
From a purely functional point of view, Comecer incubator meets the strict performance requirements defined by DIN 12880:2007-05, the current standard for the testing and validation of incubators, ovens and fridges.
DIN 12880:2007-05 dictates to experimentally characterize the incubator for the points listed below.
Thus, Comecer incubator has been finely tested in response to these requirements:
1. Determining the heating and humidification times
The DIN 12880:2007-05 standard indicates that the heating and humidification times are considered as completed once the actual value parameter in the middle of the working chamber volume permanently remains within the limit deviation specified.
The heating and humidification times have been measured by launching the incubator in its operative mode and on-line monitoring the main CPPs.
For avoiding condensation phenomena, the humidification phase is started only when the target temperature is firmly reached.
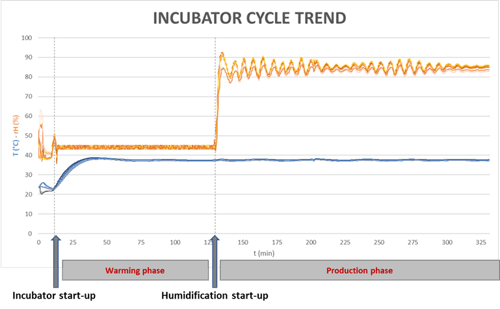
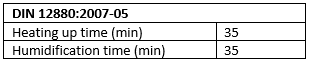
Temperature and relative humidity homogeneity has been tested by taking advantage of nine calibrated data-logger placed in a uniform manner with the aim to cover the entire incubator volume (50L).
The table below shoes the maximum spatial and temporal deviation recorded among the loggers:
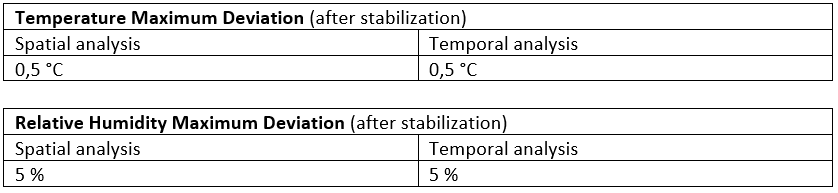
3. Measuring the recovery time after door opening
Once stabilized in its parameters, the incubator door has been opened for 30 seconds and closed.
The recovery time required for compensating the drop in temperature and relative humidity has been measured:

Finally, Comecer incubator meet the major requirements of current ATMP production approaches in accordance with the cGMP guidelines.
Moreover, it functionally respects the strict performance dictated by the DIN 12880:2007-05 standard.
Discover all of Comecer's ATMP solutions
Learn more about our ATMP - Cell and Gene Therapy manufacturing solutions
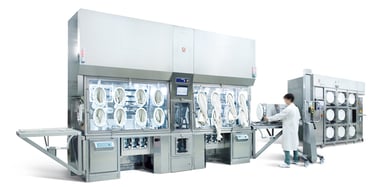
Download the full incubating system PDF
Fill out the form to download the entire pdf document: